The engineering staff at Porbeck Engineering Corporation is proficient in the use of engineering design software including finite element analysis, piping stress analysis, network flow modeling for compressible and non-compressible fluids, structural analysis, and high definition laser scanning. The company maintains current versions of all design software.
TECHNOLOGY
- Services – Record drawings, retrofit designs, non-licensed surveys, conceptual design, construction documentation
- Safety – eliminate or reduce the need for scaffolding, fall protection harnesses, and proximity to temperature and/or chemical hazards
- Time – quickly gather field information, reduce the need for return trips to get missed information or check questionable measurements, allows data collection without equipment shut-down or cooling
- Accuracy – greatly improved accuracy over traditional field measurement techniques
- Integration into 3D models and free viewers for efficient and easy client reviews
- Quickly check new equipment and piping in the point cloud or corresponding 3D model for conceptual feasibility and interferences
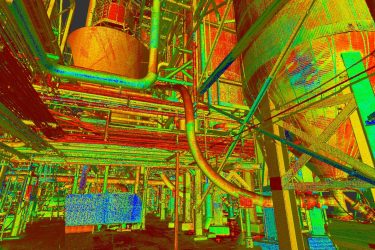
Point cloud registered from project scans
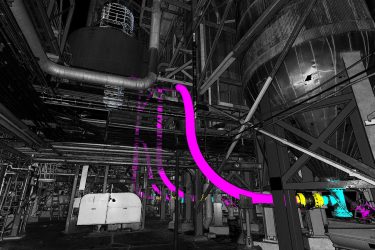
Point cloud “real view” with modeled blow line piping
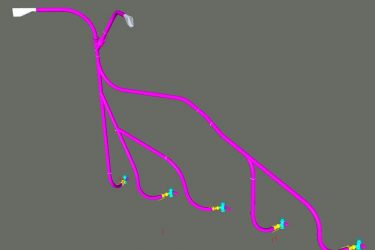
3D model used to create 2D fabrication
drawings of the entire system
Porbeck Engineering routinely uses FEA to simulate real world behavior. This powerful software has the capability to perform linear, static, and thermal analysis including static fatigue, heat transfer, linear buckling, and linear statics. Advanced analysis includes frequency response, impact analysis, random vibration fatigue, automated drop test, transient response, and other advanced features. PEC uses this software for analysis of existing structures and new structural designs, tank design and analysis, complex piping systems including lined piping, heat transfer calculations and resulting thermal stresses, and other complex systems requiring finite element analysis.

FEA Model of a Partial Condenser
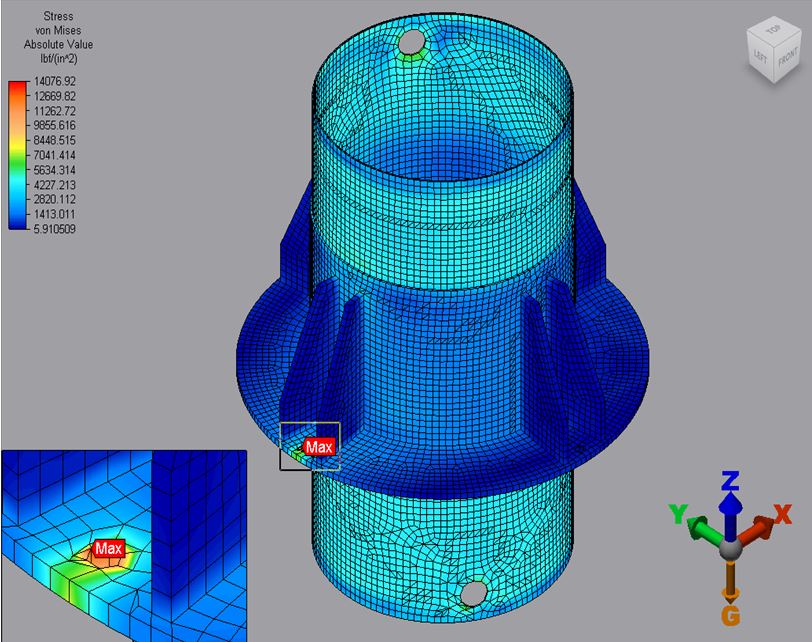
Von Mises stress results for existing shell,
new repad, and new support ring
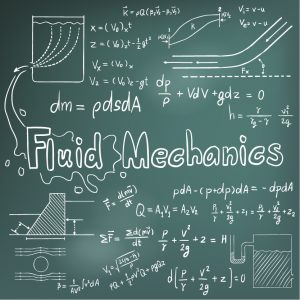
PEC has been using one of the leading fluid analysis software programs to perform liquid, compressible, and stock flow piping designs for nearly 30 years. PEC began using this software early in the program’s development and helped troubleshoot early versions and provided feedback for design improvements. This product allows us to design new piping systems and troubleshoot existing systems. With over 6000 pre-programmed fluids, and the ability to create custom fluid profiles, our engineers use this software to size new pump and piping systems, create pump specifications and work with pump vendors to make the best selection for each specific application. PEC has many years of experience helping clients troubleshoot their existing fluid systems. Whether it be pressure and/or flow rate issues, we can help identify the problem and communicate this to our clients through detailed reports and graphic representations to provide solutions.
Porbeck Engineering routinely uses our pipe stress analysis software to perform complete static and dynamic piping analyses, check designs for compliance with required piping codes and guidelines. This software allows us to verify that new piping design systems meet the associated codes, as well as analyze existing piping systems to help our clients troubleshoot problematic areas.
PEC has engineers and designers proficient in the use of multiple 3D design modules. These products offer professional-grade 3D mechanical design and product simulation tools which allows our firm to provide a wide range of engineering design services ranging from complete new plant designs, detailed machine design and fabrication details, animated mechanical videos, and much more. This technology allows employees without a technical drawing background to better visualize and comment on proposed project designs. We have the capability to import vendor supplied 3D equipment drawings from multiple formats to integrate into our 3D models. This software also allows for simpler structural and piping design as well as integration with point clouds generated from our 3D high definition laser scanning services. We have the ability to develop and integrate P&IDs with the 3D plant model, orthographic drawing production, and isometric drawing production including an automated Bill of Materials report.
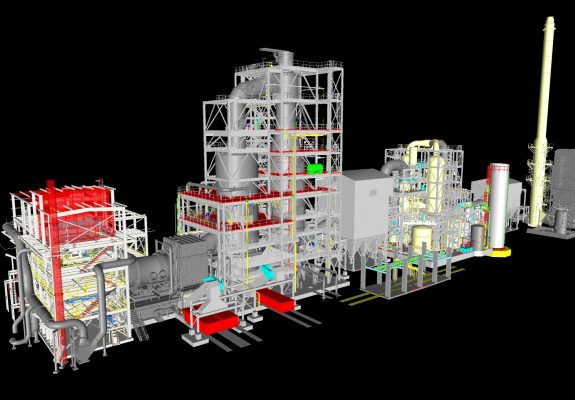
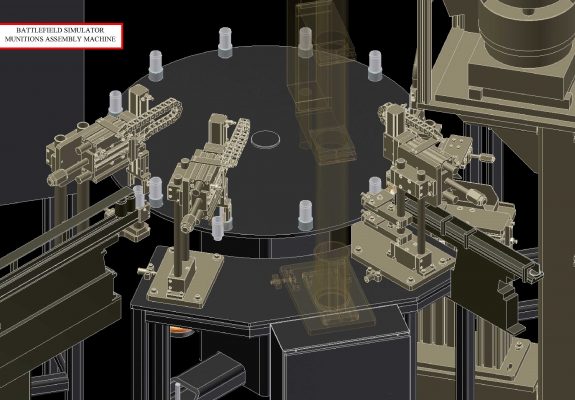
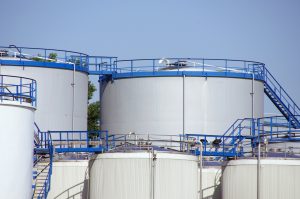
At Porbeck Engineering we use tank design software along with finite element analysis to design new storage tanks, certify existing tanks as fit for service based on licensed third-party inspection reports, and provide scope of work descriptions for required tank repairs. We are familiar with the various API codes governing tank design and repairs. We have extensive experience with the different tank applications in the pulp and paper and hazardous waste industries.